MVP Lab Report – May 2024
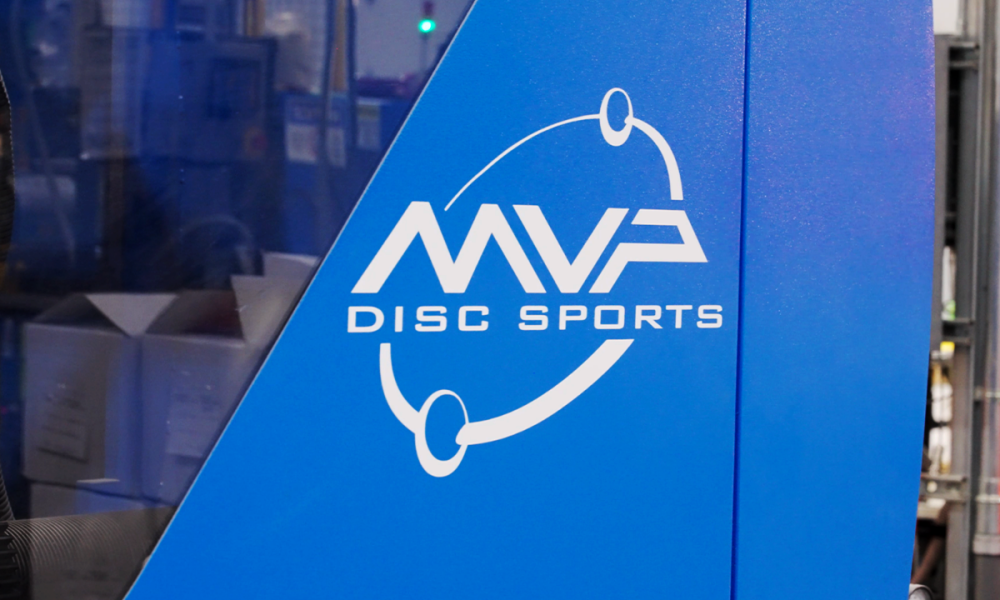
Greetings GYROnauts!
It’s time for us to put out a very long overdue MVP Lab Report! It’s been another wild year for MVP so far, especially as we started out the new year in our new warehouse. We continued to further expand our production capacity to meet the unprecedented market share growth we’ve experienced since the historic signing of Simon Lizotte followed by the signing of Eagle McMahon. I also want to share some exciting news with regards to Electron plastic and clarify many of the recent FAQs surrounding the recent recipe change with the launch of the Pixel. I’ll break this Lab Report into each of these mentioned topics.
New Warehouse Move
The move into our warehouse at the end of December 2023 was a much bigger-than-expected project, but it continues to go smoothly. Even until now in May 2024, the process of moving into and organizing our new warehouse is still undergoing. However, we’re finally in the latter stages of the project, and we couldn’t be happier with the final result.
Why did it take so long? As you might have noticed in the Eagle Announcement video, our warehouse was in quite a state of disarray at the start of 2024. Only weeks prior to that we relocated more than 70 semi-trucks from a temporary warehouse, a task that was completed within a remarkable 2 week timeline. While our pallet racking was ordered months prior, much of it was specialty pallet racking with a 4-5 month lead time. That means our pallet racking didn’t arrive until February/March. While it would have been ideal to have pallet racking in place before relocating the warehouse, it simply wasn’t going to be practical to do so after the Eagle Announcement or when the Spring Season was underway.
Since that time, the majority of our pallet racking has been installed in the new warehouse. Our shipping line was also moved and expanded within the new warehouse. We continue to refine and adjust operational layouts for the most optimal workflow in our warehouse operations, and we’re finally starting to get everything honed in.
Another benefit to our new warehouse is that the additional space can be utilized for initiatives like our recycling program. The new warehouse allowed us to implement a new recycling program to bulk collect and sort recyclable materials to further minimize our environmental impact. In only a few short months, we have already diverted 17 Tons of Materials from the landfill (in addition to what has been saved with the implementation of the R2 Neutron line).
Production Capacity Updates
A new warehouse alone will not solve all challenges with keeping up with the new level of demand. Obviously, expanding production output is equally as important as the new warehouse. The new warehouse has helped tremendously with that effort, but those efforts have been underway since we signed Simon Lizotte at the start of 2023. Technically 2020-2021 were also big years for our production ramp-up, but that progress slowed in 2022 with a market correction (almost every disc golf company felt a correction in 2022 post-COVID when market conditions normalized).
Even with that brief pause in our ramp up, the process of ramping our capacity back up to 1000% of our pre-COVID levels has taken years. Why does this process take so long? The main issue is the lead times of equipment. Much of the equipment we use in our production is leading edge plastics technology, so much of it has extremely long lead times. The typical lead time for much of our plastics equipment has been 5-6 months. Multiply by that dozens/hundreds of plastics equipment, and you arrive at what takes years to build out a leading edge plastics facility. Sure, there are plenty of options of plastics equipment out there that are in-stock and readily available, but we prioritize quality over everything else.
In addition to the long lead times, the equipment is extremely sophisticated and interconnected as a single complex system. The complexity of the equipment we’re installing requires a vast amount of time to assemble, integrate, hookup utilities, calibrate, debug, make engineering revisions, and continue the ongoing process optimization. Therefore, even considering that we’re ordering equipment months in advance, there’s several more months of installation required to get the systems to optimal operational status.
At long last after so many years, we have finally achieved a production capacity sufficient to meet our demand. Does that mean product availability on our order form will finally open back up? Yes and No. Yes, our order form will recover in availability for both Wholesale and Custom offerings. However, with hundreds of products in our catalog, it will take many months for that recovery to fully take place. Nevertheless, we can assure all retailers and custom stamp customers that options will continue to improve in the coming months. We were close to having an order form recovery late 2022, but the historical signing of Simon Lizotte in 2023 quickly reversed that, therefore kicking our efforts back into overdrive to ramp up our capacity once again to where we finally are today.
As part of our effort to expedite the process of recovering our order form availability, we will continue to follow a “Make-To-Order” for a while. This means that lead times for retailers will still be weeks, but we feel that optimizing our production schedule to increase product availability is well worth the trade-off of extended lead times. We’re producing products at record numbers and we’re confident that product availability will reflect that in the coming months.
Electron Plastic Updates
I always like to save the best for last! I wanted to provide some clarification and updates on the FAQ about Electron Plastic.
Electron plastic underwent some changes upon release of the Electron Pixel. In particular, we softened up the blend of Electron plastic to what we felt was a more appropriate standard of flexibility for Soft, Medium, and Firm. Making Electron plastic softer is actually much more challenging than it sounds. In GYRO overmold discs particularly, injection pressures in the several thousands of PSI need to be used to inject molten plastic to bond onto itself. These immense pressures pose significant challenges during the overmold process, particularly deformation of the center core made with a soft plastic that will damage merely upon the impact of a tree-hit. Some considerable engineering changes were needed in the process to open up our processing window to make softer Electron plastic possible. In solo-molds, Electron plastic is a breeze! However, our quest for continuous improvement and progress has made it possible to consistently make Electron plastic softer and grippier in GYRO Technology.
One detail that I feel is important to clarify is that the changes undergone in Electron plastic were merely a recipe change. The “ingredients” (i.e. the base materials) have remained unchanged for many years.
With that being said, in the background we have been ramping up our R&D efforts in Electron plastic, and we have a handful of new candidates for Electron material options. As alluded to in a previous GYROPalooza Lab report, we intend to launch an experimental plastic series via the MVP Pro Shop to serve as a platform to offer prototype plastic blends and collect feedback on these new material options. In fact, these types of experimental offerings were one of the main objectives of the MVP Pro Shop (in addition to supporting Team MVP and Artists).
Why not offer these experimental blends through our network of retailers? The demand necessary to supply retailers is much higher than what it typically needed to conduct experimental plastic and mold trials. When MVP Pro Shop was in a state of construction last year, you may recall the Simon Line prototype Time-Lapse being extremely limited to retailers (every retailer was limited to only 10 units). Even with that extreme limit, the volume needed to supply retailers is nearly a production quantity and pushes the limit of what really is a “prototype.” In summary, prototypes typically produce hundreds of units at a time, but supplying retailers requires many thousands of units (even with limits in place).
The MVP Pro Shop will continue to be our outlet for experimental offerings and gathering market feedback, but our valued network of retailers will remain the prime source for stock and special edition offerings. Disc Golf retailers play a crucial role in the growth of disc golf by fostering a community in their local scene, and we will continue to offer them our maximum support. If local brick and mortar retailers are no longer available, then the local communities associated with them are lost as well. Manufacturers selling stock products direct-to-consumer has severely harmed other industries (e.g. Skateboarding), and we’re determined to not let that happen to the amazing disc golf community. As such, we always encourage everyone to support their local retailer for their disc golf needs first and foremost.
We will delve into the specifics about the experimental Electron series coming in a later report, but I am excited to finally announce this series now that we have an MVP Pro Shop website we’re satisfied with. We hope to have some further updates about the details of our Experimental Electron series later this summer.
Conclusion
Last but not least, I want to thank the incredible team we have at MVP. Every department in the company has continued to step up to the challenges with determination and dedication, and for that I am extremely grateful and want to make sure they get the recognition they deserve!
Thanks again for all of your support which has enabled us to continue our mission of being The Leading Edge™ in disc golf technology.